Чем лучше работаем, тем больше бережем

По итогам первого квартала победителем по энергосбережению среди основных цехов завода стал второй сортопрокатный цех. Мы поговорили с заместителем начальника СПЦ-2 Марком ГИНЕЙКО о том, что помогло коллективу добиться хороших результатов.
— Марк Викторович, давайте сразу озвучим цифры. Сколько удалось сэкономить СПЦ-2 на энергосбережении?
— В первом квартале СПЦ-2 был загружен заказами. Мы отработали все действующие контракты. Было произведено 140 тысяч тонн проката на горячей части, и за счет этого вся потребленная электроэнергия по удельному расходу на тонну продукции дала неплохой результат. Если показатель удельного расхода для нас был доведен 141 киловатт на тонну произведенной продукции, то по факту мы получили 131. В денежном выражении это 340 тысяч рублей. По газу более скромные результаты — 100 тысяч рублей экономии. Итого 450 тысяч рублей мы внесли в копилку завода.
— То есть надо соблюсти некий баланс между количеством тонн и потребленной электроэнергией?
— Энергосбережение и энергопотребление — ключевые показатели в отчетности. Энергетический баланс в прокатном производстве зависит от количественного состава используемого оборудования в единицу времени для производства того или иного вида продукции. К примеру, при производстве малых типоразмеров задействовано практически все оборудование. Соответственно, потребление электроэнергии максимальное. Если же мы катаем большой диаметр, например, 80-й круг, — степеней обжатия гораздо меньше, значит мы затратим в единицу времени меньше электроэнергии. С точки зрения потребления газа нагревательная печь в обоих случаях работает в своем технологическом режиме и тратит примерно одинаково.
— Получается, что энергопотребление зависит от сортамента?
— Да, мы очень сильно зависим от сортамента. Если брать наш цех, то на месяц формируется так называемая норма удельного потребления электроэнергии на одну тонну продукции. Чем больше произведем прутка, т.е. более крупного товара, тем она меньше. А если больше надо произвести продукции с линии катанки, т.е. более мелкого профиля, то норма увеличивается.

— Можно ли в таком случае как-то влиять на энергопотребление, чтобы снижать расход электроэнергии?
— Конечно, можно. Мероприятия по энергосбережению могут быть как техническими, так и организационными. Есть такие, которые мы выполняем из года в год постоянно, есть новые, которые мы разрабатываем, видя определенные резервы. Из последних текущих мероприятий — оптимизация режимов работы оборудования, которое обеспечивает основную технологию. Специалистами цеха было определено, что во время проката можно оптимизировать работу гидравлического оборудования. Нашли возможность доработать автоматику и не включать всю группу насосов без необходимости. С момента пуска цеха нашими специалистами ведется постоянная работа над усовершенствованием технологических процессов, касающихся режима работы печи по температурному диапазону нагрева материала. Чтобы не получить перегретый металл, а нагреть его до определенной температуры, и чтобы он был пластичным и получилась правильная геометрия. Это немалая толика по части экономии газа.
— А тренд на дифференцированный тариф по оплате электроэнергии еще сохраняется?
— Да, это актуально. Предприятие оплачивает электроэнергию в зависимости от периода потребления. Наиболее пиковое время — с 8 до 11 часов. Один час работы в пик приравнивается по оплате к четырем часам работы в ночное время. Поэтому мы отдаем преимущество в эксплуатации оборудования ночному периоду, а в пиковый период планируем различные мероприятия технического плана, связанные с остановкой стана.
— Освещение к каким затратам относится?
— Это условно-постоянные затраты, направленные на собственные нужды. Жизненная необходимость, если можно так выразиться. В одном только производственном корпусе СПЦ-2 почти 1,5 тыс. точечных светильников потолочного освещения, каждый из которых оснащен газоразрядной лампой высокого давления мощностью 400 Вт. На период проектирования и строительства цеха (2013-2014 гг.) это было оптимальным вариантом, т.к. каждый источник света в виде энергоэффективных светодиодных компонентов имел высокую стоимостную долю. Промышленная LED технология только набирала обороты. Поэтому тогда спроектировали и установили газонаполненные источники света. Сейчас поэтапно переводим цех на светодиодное освещение. Это мероприятие рассчитано на пять лет, т.к. одномоментно заменить общее количество этих лампочек на светодиодные довольно дорого. По расчетам планируем получить четырехкратное снижение потребляемой электроэнергии по освещению в сопоставимых технических условиях. Но это у нас впереди.
Марина БОЖИНСКАЯ
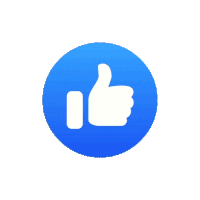

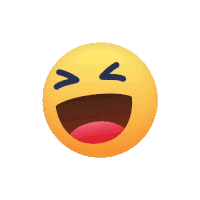
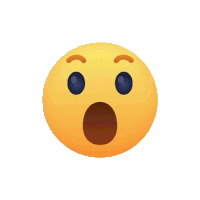
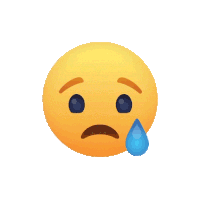
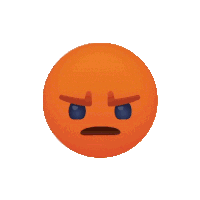